Streamlining Government: How Lean Manufacturing Principles Could Revolutionize Presidential Efficiency
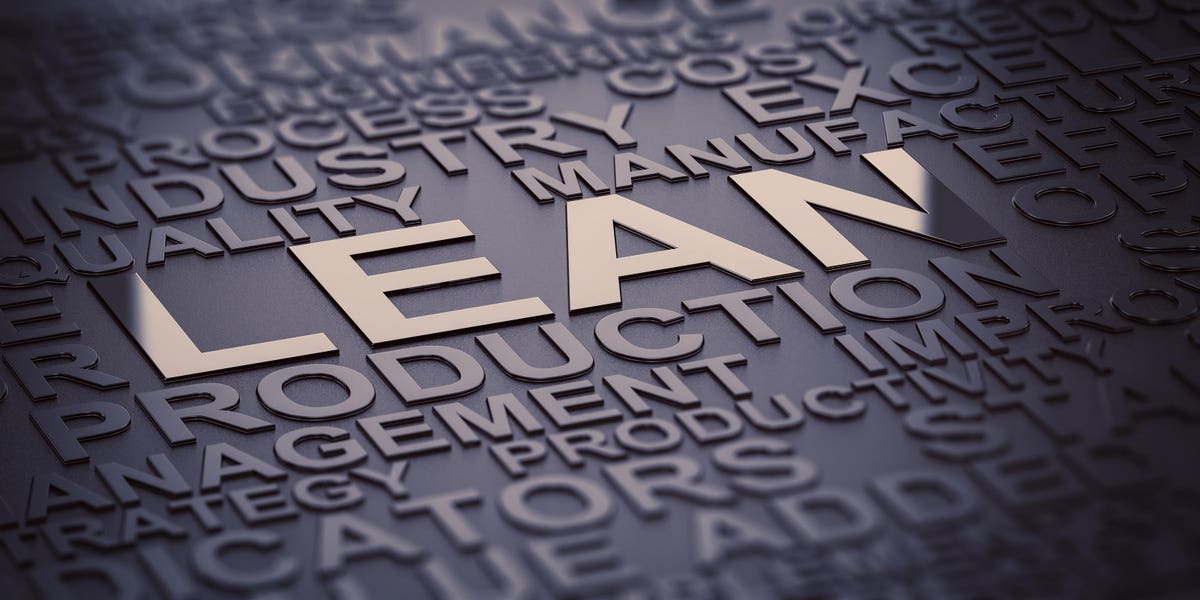
Mastering Efficiency: The Power of Lean Manufacturing Principles
In the world of modern manufacturing, savvy companies have discovered a transformative approach to production that goes far beyond traditional methods. Lean manufacturing isn't just a strategy—it's a philosophy of continuous improvement and waste elimination that can revolutionize how businesses operate.
At its core, lean manufacturing is a versatile methodology that transcends industry boundaries. Whether you're running a high-tech assembly line or managing a service-based operation, the principles of lean thinking can be applied to streamline processes, reduce unnecessary expenses, and maximize overall efficiency.
The beauty of lean manufacturing lies in its universal adaptability. From reducing excess inventory to optimizing workflow, these principles offer a comprehensive approach to operational excellence. Companies that embrace this methodology don't just cut costs—they create smarter, more responsive, and more competitive business models.
By focusing on value creation and systematically eliminating waste, organizations can unlock unprecedented levels of productivity and innovation. Lean manufacturing isn't just about doing more with less—it's about doing things better, faster, and more intelligently.